This series follows my attempt to develop a product that I dream of getting into the elite levels of hockey. Previously on the Quest: Part 1, Part 2, Part 3, Part 4, Part 5, Part 6, Part 7, Part 8, Part 9, Part 10, Part 11, Part 12, Part 13, Part 14, Part 15, Part 16, Part 17, Part 18, Part 19, Part 20, Part 21, Concept Launch, Part 22, Part 23, Part 24, Part 25, Part 26, Part 27, Part 28
You rejoin me in the midst of my noble quest to make sure that the Uncage won’t flex back into goalies’ faces.
Last time, I’d narrowed down the issue to an outer frame that flexed too much like a closing clamshell.
To fix that issue, I had two paths open to me. The first was reasonable and rational and would be quick to implement. The second was more challenging but also more fulfilling. Of course, if I was reasonable and rational, I wouldn’t be doing this project at all, so you can already guess which path I took.
But for the sake of completeness, the first path would’ve been to abandon the floating crossbar design, where the crossbar is only attached to the outer frame by way of ropes. Instead, I would weld the crossbar to the outer frame, preventing the crossbar from moving at all. And I’d add a vertical bar, like the one in my very first concept, which would prevent the clamshell motion.
Straightforward, simple, and almost guaranteed to work. But also a little boring.
What’s the point of being in charge of my own time if I’m not going to pursue interesting ideas? A viable business in a timely manner? Come on now. So I took the second path and stuck with the floating crossbar.
Besides it being the more interesting path, I had two other reasons for sticking with the floating crossbar. First, the indirect connection via the ropes should cushion the crossbar from the impact of the puck. That should allow me to use a thinner crossbar and provide better visibility for goalies. Second, and this is still very hypothetical, but that cushioning could potentially be a positive for concussions.
The fact that other sports have been going in that direction is encouraging.

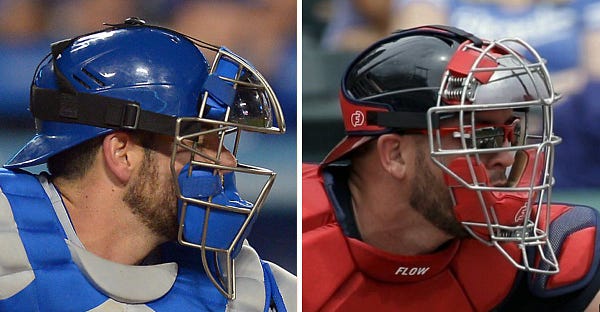
Anyways, that’s enough of the justifications. On to the stiffening.
If you want an in-depth, technical writeup of what makes things stiff, feel free to read this post I did a long time ago when I was working on a different project. But the one sentence version is that the most efficient way to make something stiffer is to make it thicker (like corrugated cardboard or I-beams).
For the mask, the simplest solution would be to increase the diameter of the frame, but the frame is already hefty as it is. Any bigger and it would start looking a little dumb (an important factor for goalies) and also provide a bigger surface where a puck could get caught, rather than deflecting smoothly away.
So what else could I do? I could add gussets, a well-established way to stiffen corners.
A very good solution, but one morning I thought I woke up with even a better one. The idea was essentially two thinner bars offset from each other, a lot like the top bar on football helmets.
This would essentially give me the “thickness” of a larger diameter tube but just in the direction I needed it. Not only that, but the ladder-like design would be ideal for cleanly anchoring the ropes that make up the rest of the cage. In theory, a very tidy design. Here’s the model I mocked up for my cage.
Making a physical prototype would’ve required me to buy a new tube bender for the smaller radius tube, bend a bunch more tubes, get many more joints welded, etc, so I looked to computer simulations instead.
The upside of simulations compared to physical testing is clearly the speed at which you can iterate through concepts. But that speed made me feel like I didn’t have to think so hard about the reasoning. As soon as a half-formed idea came to mind, I adjusted my 3D model and simulated it. Dozens and dozens of times. It was a game to win, something that could be optimized to no end, and a total time sink.
The double tube version, in particular, got me. The simulation showed that it wasn’t a very good solution but I just loved the idea so much. By my moment of inertia calculations, the double tube version should’ve been twice as stiff as my baseline. But instead, the simulation was showing it was a lot less stiff.
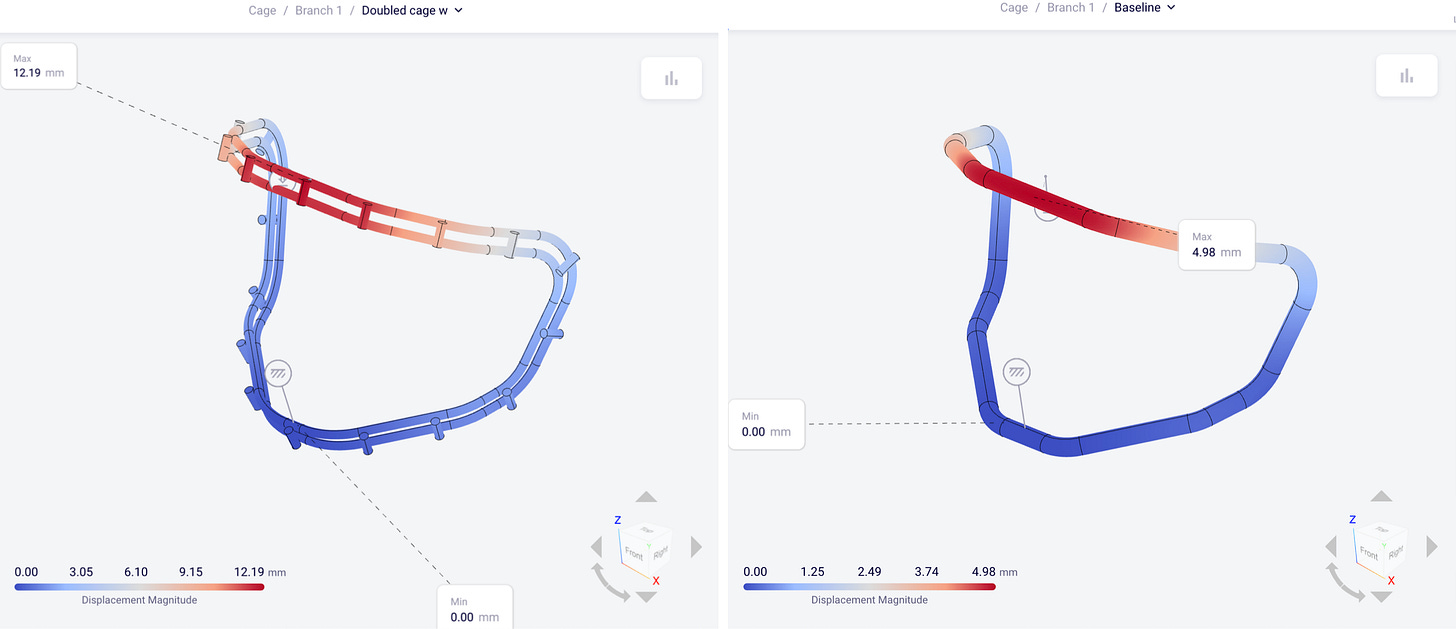
Though the double tube frame was very stiff in one direction, it was pathetically floppy in the other, so the whole thing was getting twisted. I could continue iterating and fix it, but I realized it just wasn’t worth the time. I still have a lot to do and getting a perfect frame probably isn’t the best use of my time.
Will I spend Thanksgiving – when I’m away from my garage – furiously trying to make my beloved idea work? Quite possibly.
But for now, a gusseted frame would be the way to go. Easy to make, a lot stiffer, and not much heavier than my baseline. I cut out some sheet metal with tin snips, bashed the pieces with a hammer until they wrapped around the frame, and then glued them down with JB Weld.
That wasn’t the only change I made.
There are two factors in how much something flexes. The stiffness of that something and force applied to that something. I’d already improved the stiffness, but could I reduce the force (without asking everyone to shoot the puck more slowly)?
I thought I could. Not reduce the force exactly, but redirect it.
By changing the orientation of the the ropes, I could change the direction of the forces going into the frame. A puck hitting a rope will cause a certain amount of tension in the rope. That tension does not change based on the orientation of the rope (for direct impacts). But the orientation does change how the frame responds to those forces.
A rope oriented straight down pulls straight down on the top bar of the frame, leading to that clamshell motion I’ve been trying to eliminate. An angled rope will pull just as strongly, but part of that force will be directed along the frame tube. There will be a smaller net force trying to clamshell the frame.
If you want to feel this, try putting a rubber band around your index fingers and pulling your hands apart until there’s some tension in the rubber band. Notice how that feels. Now pull one of your hands towards you a few inches. Notice the difference. Instead of just pulling straight apart, you’re also having to apply some force towards / away from you. But the force you use to keep your hands apart should be lower (if you haven’t stretched the rubber band like crazy).
That was the theory at least and, to cut a long story short, the tests seem to agree.
There will of course, never be zero deflection. But I finally seem to be nearing that perfect zone – a little give to (hopefully) absorb some energy but not so much to smack a goalie in the face.
Thanks as always for reading,
Surjan