An Inventor's Quest for the NHL Pt. 26
Embracing Failure, or at Least, Giving It a Quick Side Hug
This series follows my attempt to develop a product that I dream of getting into the elite levels of hockey. Previously on the Quest: Part 1, Part 2, Part 3, Part 4, Part 5, Part 6, Part 7, Part 8, Part 9, Part 10, Part 11, Part 12, Part 13, Part 14, Part 15, Part 16, Part 17, Part 18, Part 19, Part 20, Part 21, Concept Launch, Part 22, Part 23, Part 24, Part 25
It’s long overdue, but I owe an apology to Sir James Dyson. In my very first post on this newsletter, I commented on how ridiculous it was “that a man has been knighted for his work with vacuum cleaners.” The deeper I get into this invention business, the more my opinion has changed. It hasn’t become more biased mind you, just more seasoned and professional. Now, in my very professional opinion, anyone who successfully invents anything should get a knighthood.
It’s not easy! As Dyson said, “I made 5,127 prototypes of my vacuum before I got it right. There were 5,126 failures.”
Last month, I started believing that all my failures were behind me. That’s why that failure at the puck shooting machine in San Jose hit me so hard (and why I’m still talking about it). I think I’ve finally accepted where I am. I had a concept launch that went way better than expected and allowed me to keep working on this project. But it was a concept. There are still plenty of failures ahead of me before I get it fully right. I’m trying to change my attitude and see those inevitable failures as markers of progress rather than evidence of impending doom.
This week, I put a few more of those failures behind me.
Last we checked in on the cage, it had broken two different ways. First, the Dyneema rope broke where it turned a corner. The bend radius was too small and rope doesn’t like to take sharp turns. Second, in trying to solve that problem, I made my splices shorter. On impact, those splices came apart. (Not enough friction to hold together.)
So I needed a solution where the rope had gentle bends while also having enough room for full-length splices. The idea I eventually came up with was pretty simple – little posts around which I could wrap the rope.
Turning that idea into reality was slightly more complicated. I’m not a welder and getting someone to weld dozens of posts wouldn’t be very cost or time effective. After brainstorming a few options I could easily build in my garage, I settled on a spacer bolted through the steel tube frame.
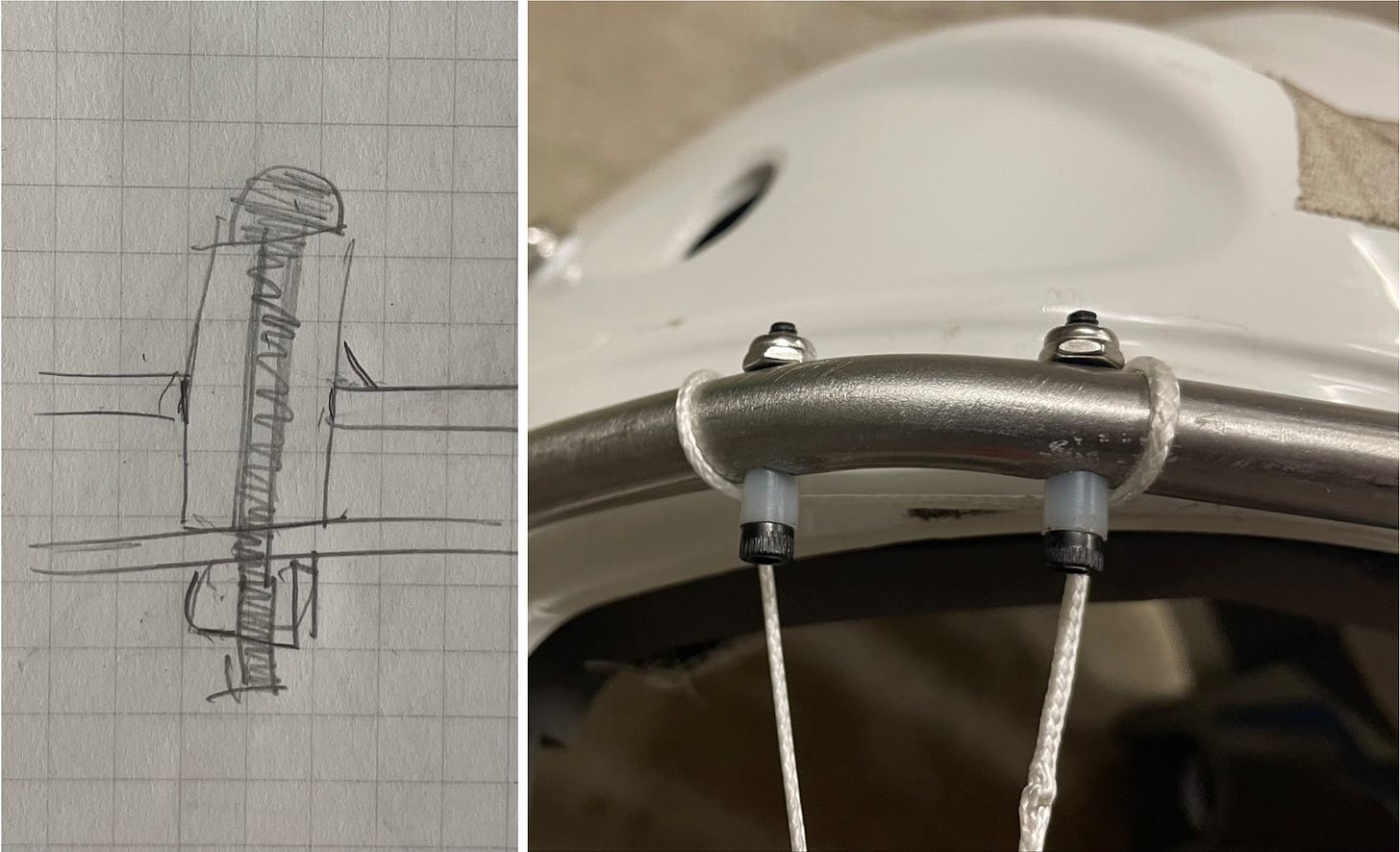
Instead of stringing the whole cage, I strang (strung?) one loop to see how the new changes would hold up.
With my new test rig, I dropped twenty pounds onto the rope from 3.25 ft – the energy equivalent of a 75 mph shot.
The rope didn’t break, but surprisingly, I bent the steel frame. It’s a little crazy to see a tiny little rope bend a hefty metal tube, but that’s exactly what happened
That’s been a common theme throughout this project – there’s never any clear good news. Here, very positive news about the rope and the changes I made. But alongside, some unexpected bending in the frame.
At this point, I got an email from Richard. (I’m lucky to have a smart, engaged readership and Richard, in particular, always has some insightful commentary.) This time, after seeing my last post about my test rig, he pointed out that my testing might actually be overkill in terms of momentum.
And it is. When I match a 75 mph shot from an energy shot, the momentum of the impact is 5x higher than even a 100 mph shot. Now, I do want my testing to be more rigorous than any game situation – but within reason.
Where’s the line between reasonable and unreasonable? Richard suggested another idea to help find that line: drop weights onto a traditional, metal cage until it fails. That would give me a more empirical sense of what combination of energy/momentum was reasonable.
I began to see some very, very slight bending in the metal cage during a test that was the energy equivalent of a 55 mph shot and a momentum equivalent of a 300mph shot. At the energy equivalent of a 75 mph shot and a momentum equivalent of a 570 mph shot, I saw serious deformation.
From that series of tests, it seems like energy equivalency is a better approximation than momentum. Either that, or the metal cages are way overbuilt from a momentum standpoint. I guess that’s possible, but I’m not going to worry about that right now. I’d rather also be overbuilt at this stage in the Uncage’s life.
With renewed confidence in my testing, I felt comfortable making a full cage with my new design concept to see how it held up.
I had a couple good tests until I hit that same 75-mph-energy-equivalent drop and then this happened.
I was using aluminum tube for the crossbar, so not surprising that it bent. (In hindsight, a bit of a lazy decision – I got tired of drilling through stainless.) The outer stainless steel frame, however, bent as well. The good news again, was that the string didn’t break. I’m aware that the bending metal probably absorbed a lot of energy, but still, I’ll take the confidence boost.
As I said in the beginning, this was about getting a few more failures behind me. And I’m liking the failures I’m experiencing more and more. To solve these, all I have to do is stiffen up the material for the frame and crossbar. Pretty easy change.
Thanks as always for reading. Join me next time to see what new and interesting failures lie ahead!
Surjan