#31 - A Composite of Milk and Linen
Casein, Flax, and a Trick from 'The Great British Baking Show'
For most, necessity is the mother of invention. For me, itchiness is.
In my quest to make a completely itch-free composite, I’ve turned to natural materials. First on the list was finding or developing a natural glue. I fooled around with hide glue and milk (casein), but didn’t feel like I had something I could build parts with. The casein felt promising, so I took that as a starting point and kept investigating.
I cast casein as the star of my show because of its versatility -- casein has been used in everything from paint to glue to plastics, so some variation of it must work for composites. But, as I’ve mentioned before, chemistry refuses to reveal its secrets to me, despite my persistent lack of effort. So I resorted to two strategies I learned in college: brute trial & error, and copying other people’s work.
I collected some promising recipes and created a few fusions. I won’t go into the details of every iteration: namely, A, B, C, D, E, F, G, H, I, J, K, L, M, N, O, P, Q, R, S, T, U, V, and W. That would be a waste of space. The majority were searches for a suitable plasticizer and the rest for additives.
I picked up the word plasticizer from one of the recipes I read. I don’t really know what it means, but it’s better that repeating “the thing that you add to break down casein and reform it into something stronger.” In my first trials, I used baking soda and Borax as plasticizers. This time around, I tried two types of lye (sodium and potassium hydroxide), pickling/slaked/hydrated lime, and triethylamine.
I’ll tell you about how those trials went in a second. But first, I should tell you that I changed the casein itself. This time, instead of making curds from milk and creating a pile of dishes, I bought casein protein powder online. I was tempted to try a chocolate-flavored one, but decided on a pure, unflavored variety in the hopes of a stronger glue. This casein was very clearly purer than the one I had isolated on my own and approximately a million times easier to work with. In fact, in my last casein-related post, I said, “What I do know is that a mixture of just water and casein stays clumpy.” Turns out -- that was wrong. A mixture of just water and amateurly-separated, impure casein stays clumpy. The purchased casein mixed smoothly with water and dried into an admirably hard plastic.
Combined with a piece of fabric though, the casein-water mixture lacked a little bit of the stiffness that I was searching for. That’s where those plasticizers come in. From what I could understand, it seemed that these plasticizers help encourage the casein molecule to link to its neighbors. The more cross-links, the stiffer the result. Lye seemed to give me the most stiffness (according to my calibrated fingers). That finding agreed with this Forest Service document, which also recommends adding hydrated lime for improved water-resistance. I’m intending to seal the part in a separate step, so I preferred the better mechanical properties of a pure lye solution.
My legal department tells me that I should add a disclaimer: if you intend to try this, please follow the proper safety procedures when handling lye. I know what you’re thinking, “Hang on a second -- you were pursuing anti-itchiness. And now you’re dealing with stuff that might not just irritate your skin, but remove it completely.”
I know it sounds completely backwards, but it makes perfect sense to me. Epoxy doesn’t require direct contact to irritate me, this stuff does. And when lye is mixed with casein, it seems safe to handle. “Seems” because I tried some on the back of my arm, where I wouldn’t have minded a little less skin, and nothing happened. Of course, I wouldn’t risk my skin without some idea of what I was getting into. Turns out that combining casein and sodium hydroxide makes sodium caseinate, a food additive added to ice cream and sausages! So not only should this lye concoction be skin-safe, but also edible. But still, probably don’t try that at home. [Agreed. --legal dept.]
What about the additives? I added everything from corn starch to Indian black salt (hoping for sulfur) to take the edge off of the casein’s brittleness, but in the end, decided it was better off without anything. The additive took too much away from the stiffness and, anyways, the lye-based glue didn’t feel as fragile as the earlier glues that had sent me down the additive path.
By this point, I was a little bored of the trials, so I decided to go bigger. I dusted off that same mold to make that same panel that loyal readers are now familiar with. I already had a new glue recipe, so logically I would just change that one variable and see how thing turned out, right? Nah. I changed the only other ingredient -- the fiber.
I had been using fiberglass, because it’s got good properties at a great price. But it has that same fatal flaw as epoxy: itchiness. So a replacement needed to be found. (Also because I like the environment.) Natural fiber composites are not a new concept -- companies are already doing cool things with hemp and flax -- but it is new to me.
The only decision I had to make was choosing between hemp and flax. According to Wikipedia, flax is a bit stiffer than hemp. Good enough for me. As I began searching for a flax-based fabric, I found out that’s simply called linen, which was much easier to source.
Fabric in hand and mold prepped, I began to mix a batch of glue. One part of lye into 35 parts of water. I used potassium hydroxide over sodium hydroxide simply because I had the potassium in flake form. (The flakes were much much easier to handle than powder.) The lye dissolved readily into the water, after which, I added ten parts of the casein powder.
On stirring, the casein clumps back into a curd-like object momentarily before the casein particles remember how much they doesn’t like their neighbors and spread out and dissolve. I had no trouble mixing the smaller batches by hand, but this larger batch hung on to a few clumps. I broke out an old stick blender and soon broke them up.
I layered fabric and glue into the mold. I remember thinking myself that the glue was a bit thick, but I didn’t do anything about it besides massaging the glue into the fabric. Three layers later, I was done.
I remembered that my last part had issues with the fabric in the corners pulling away and bridging. But how to combat that? Typically in composites, a vacuum bag is sucked down over the part to compact it down. I didn’t have anything I needed for that though, so I had to think of something else. From the Great British Baking Show, I remembered that they would fill a pastry crust with chickpeas during the blind bake to prevent it from rising too much.
Perfect. This being a Punjabi household, there was no shortage of chickpeas and lentils on hand. I covered the part in some waxpaper so it wouldn’t stick and then placed a few bags on top.
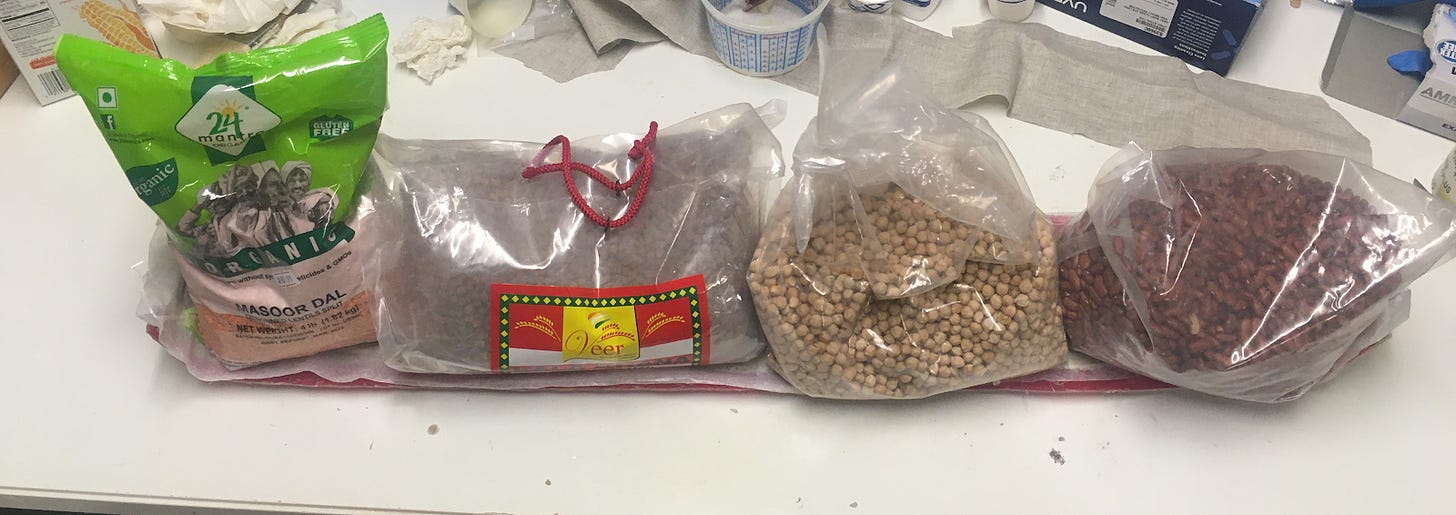
I left the part alone for two days, but when I whipped the waxpaper off, the part wasn’t cured. As I’m writing this, I’m realizing that might be because casein-based glues cure by evaporating water. I might have prevented that with the wax paper. (Further investigation is required.) I let the part sit another day without the wax paper to dry.
The result was a little limp and definitely sad, though it was cool that the glue dried clear.

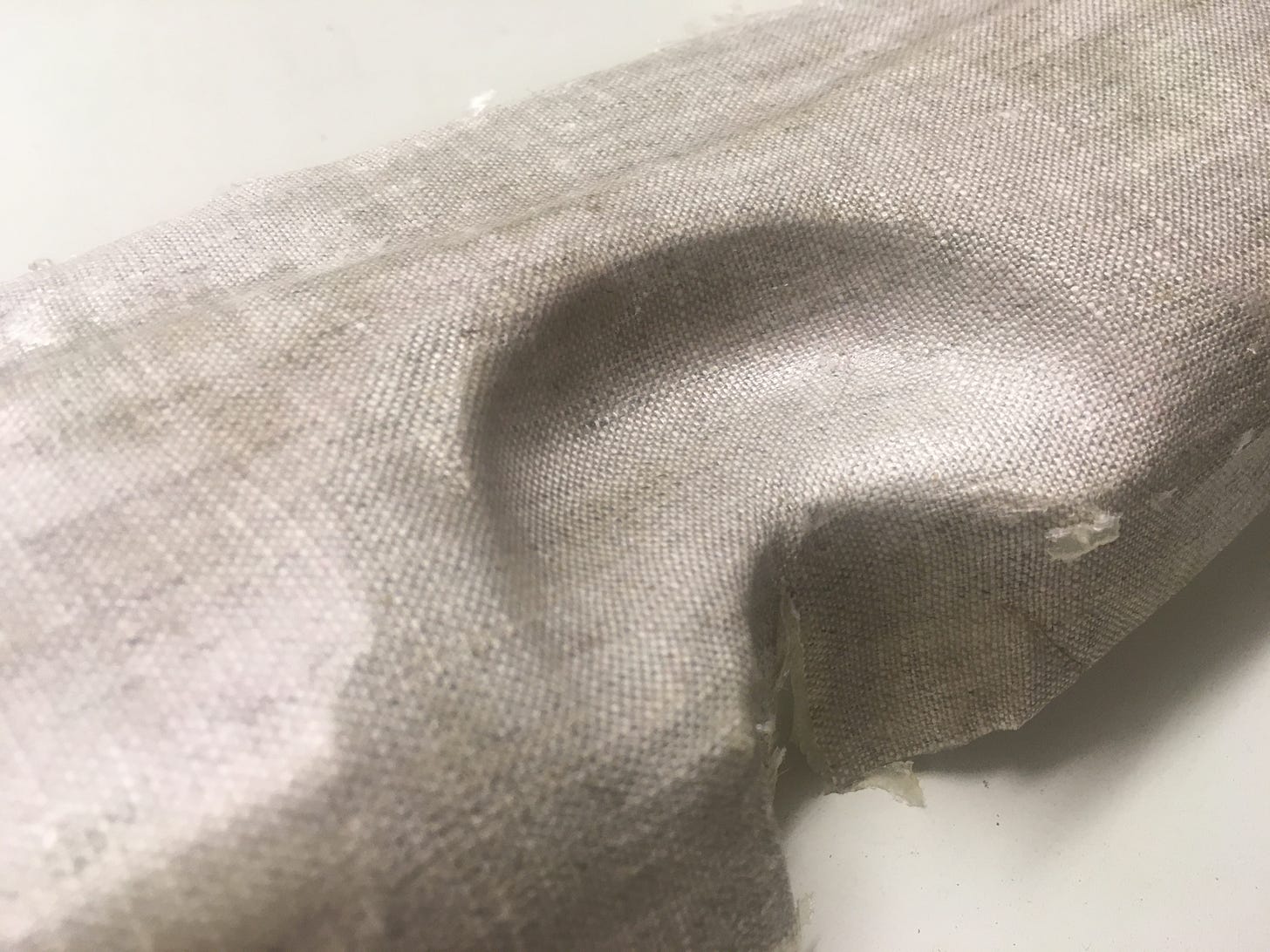
It’s clear there are fundamental issues with my method. I’m fairly confident in the glue -- I think there were other problems. I didn’t wet out the fabric completely, though I do have an idea on how to solve that next time around. The fabric is the bigger mystery. I did a direct comparison with fiberglass and it’s not even close. I was expecting there to be a bit of a drop-off but not this much. Clearly, I need to pay closer attention to the fabric -- weave, yarn, and whatever else I don’t know about. I’ll also probably have to find a way to introduce a vacuum.
I would’ve loved to have been done with this part of my project by now. This process-related stuff is boring and I’m bursting at the seams with big ideas that I want to get to. But if I take the time and get this right now, I won’t have to think about it again. That’s enough motivation.
Corrections? Questions? Comments? I’d love to have your input. Leave a comment, email me at surjan@substack.com, or find me on LinkedIn.
Drawing exercise #20. If you missed it, here’s why I’m learning to draw.
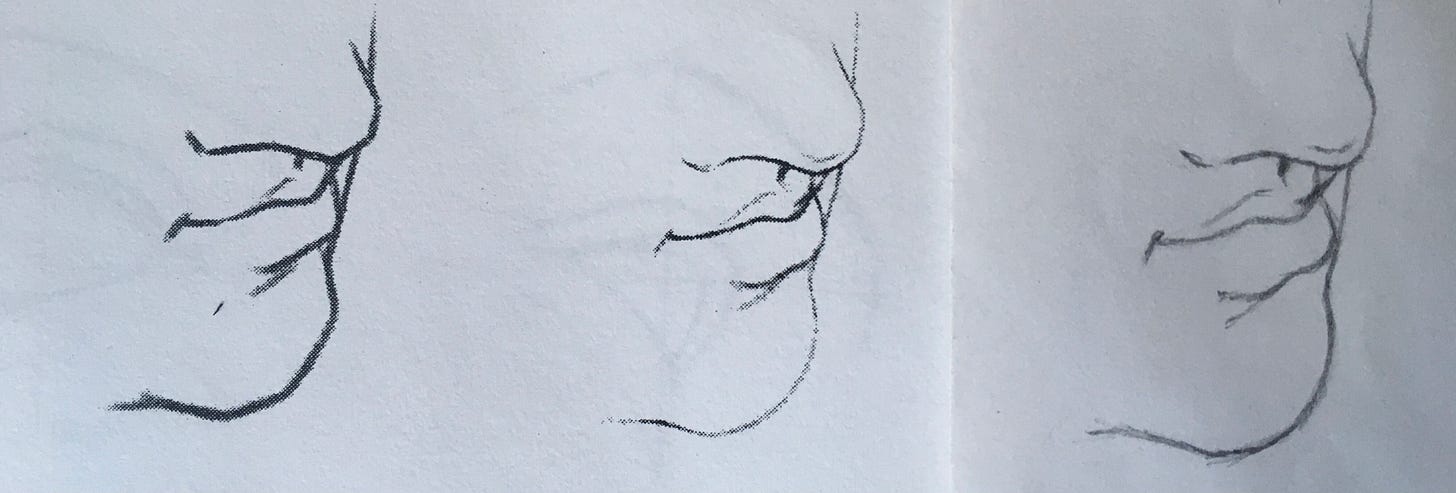
Done with a second plate!
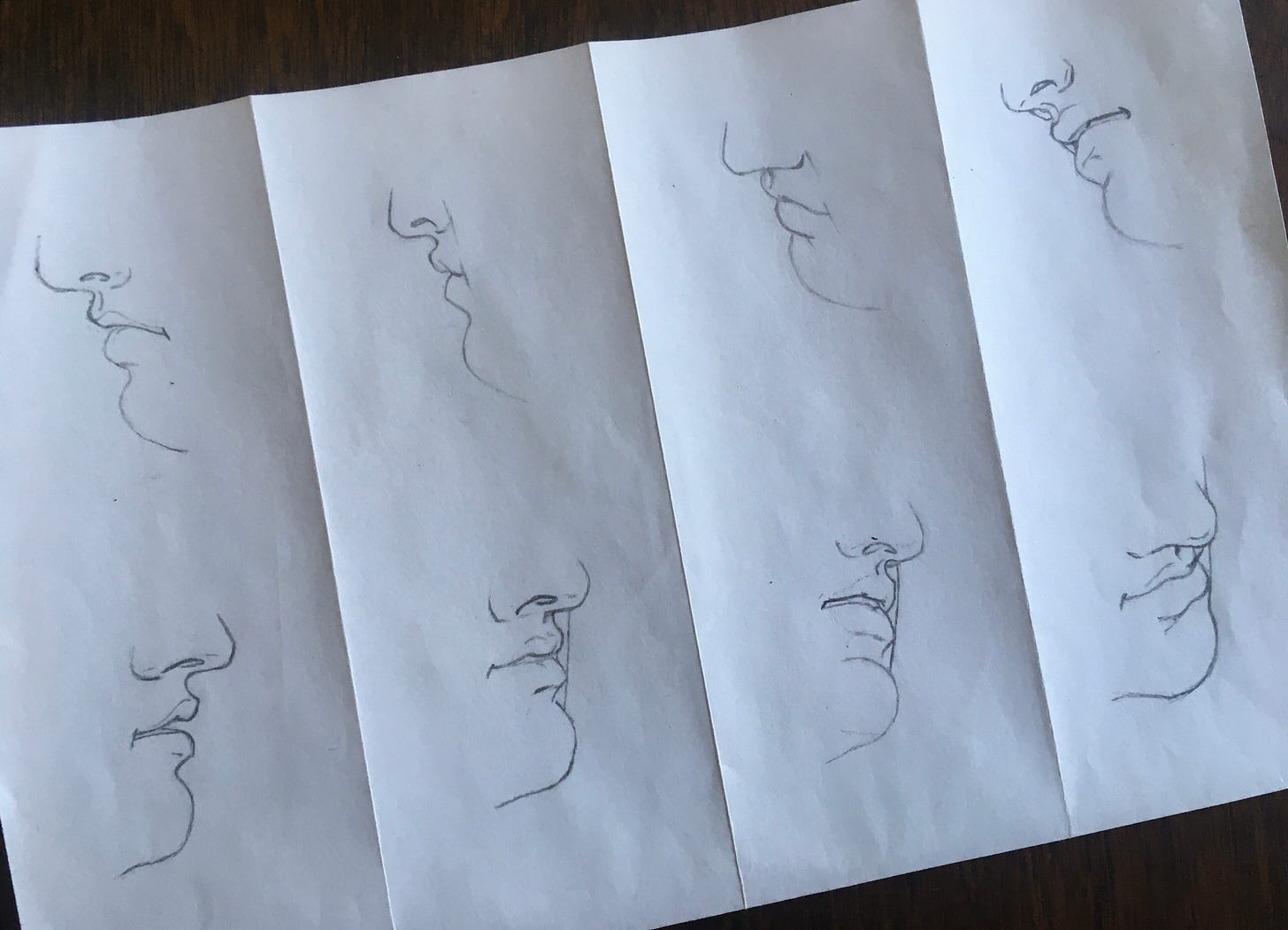