Ever since I helped design and build a Formula SAE car in college, I’ve never really had a firm grasp on stiffness. The conventional wisdom for cars is that the chassis, or frame, of the car has to be extremely stiff torsionally (in twist). Meaning that if a Hulk-version of you lifted up on the front-left wheel arch of your car, the back-left should lift the same amount (rather than sitting floppily on the ground).
The usual explanation is that you want a stable, predictable platform to allow the suspension to work as designed. I never understood why it was so compartmentalized. Why did the suspension have to take all the movement and the chassis none? Am I suggesting you go cut the roof and floor out of your car to make it less stiff? Not at all. You’d be messing with a design that has one, coherent approach towards stiffness. What I am suggesting is that there might be a completely different way to approach the design.
I did (and still do) think the idea’s a bit out there. But I got some hope in the form of historical context. In Structures: Or Why Things Don’t Fall Down, J.E. Gordon talks about a difference in Eastern and Western approaches to stiffness when talking about Chinese sailing boats:
According to our Western, engineering-school, way of thinking there is very little we can do about this [increased force from high winds], for we would rather be seen dead than allow the membrane - whether it be a sail or part of an aeroplane or whatever - to bulge appreciably between its supports…. What we actually do is make the supporting frame-work strong and heavy and expensive and hope that it won’t break - which of course it often does….
One elegant and satisfactory way of doing that has been devised by the Chinese, who, after all, have been sailing about the seas in moderate comfort and safety for a good many centuries…. The battens which cross the sails are attached to the masts and, since the whole rig is constructed from flexible materials, as the wind increases, the sail bows out between the battens…without much loss of aerodynamic efficiency.
Gordon was mostly illustrating a different point, but what stuck in my head was the two different approaches to stiffness. Maybe the need for stiffness is just driven by the dominant engineering culture. But were there other examples?
I thought of the contrast between Japanese armor and European plate armor. The Japanese variety was often made up of leather or iron scales whereas the Europeans preferred the larger, unbroken plates. Both developed around the same time and had to deal with similar weapons to start. You can visually see the difference in flexibility.
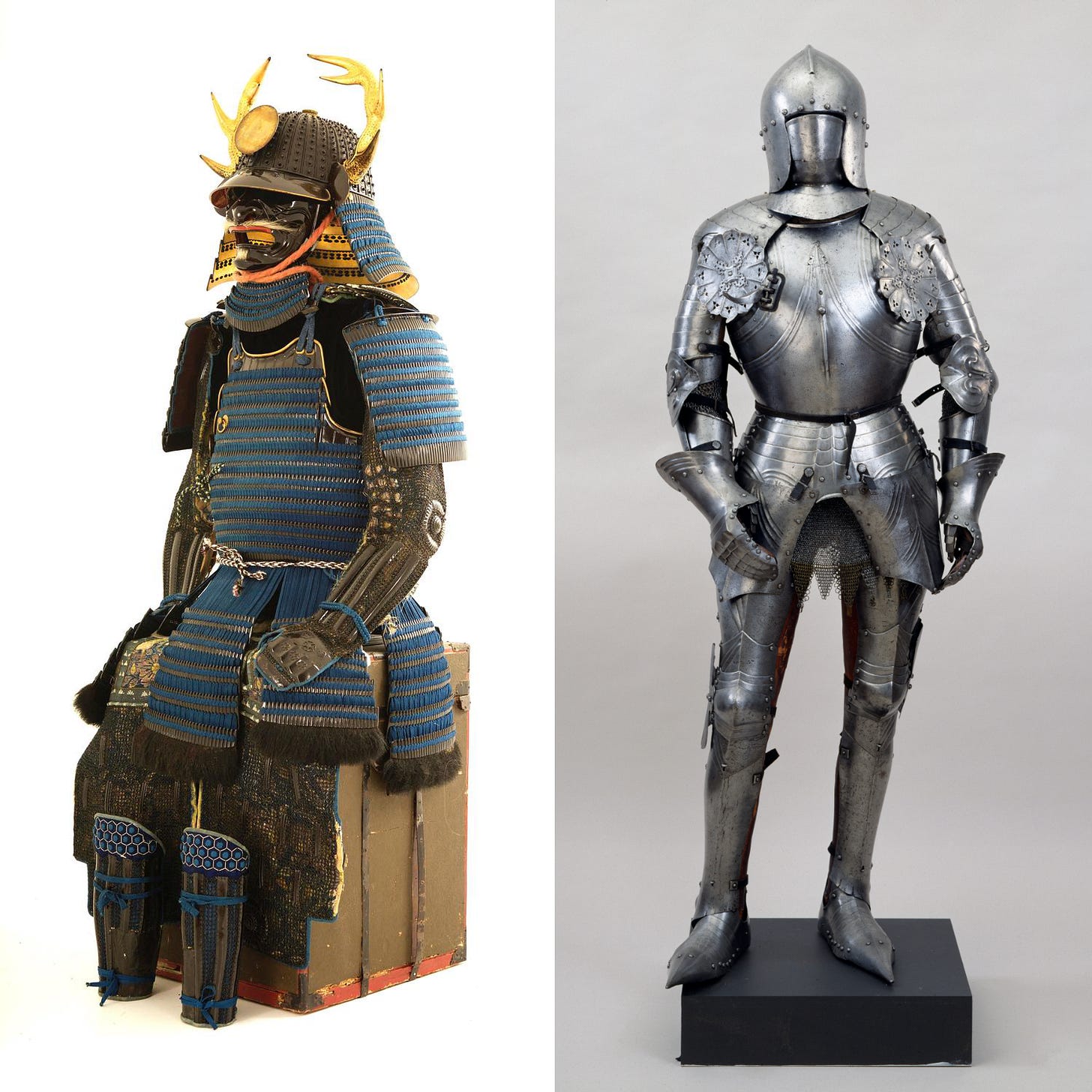
There is the near-mythical Damascus steel, a long-lost metalworking technique which people attempted to recreate for centuries. From Ancient and Medieval India Vol. 2, “The swords of the Sikhs are said to bear bending and crumpling, and yet be fine and sharp as the scimitar of Suliman.” The legend was that you could wrap a Damascus blade around your body and it would spring back to its original shape.
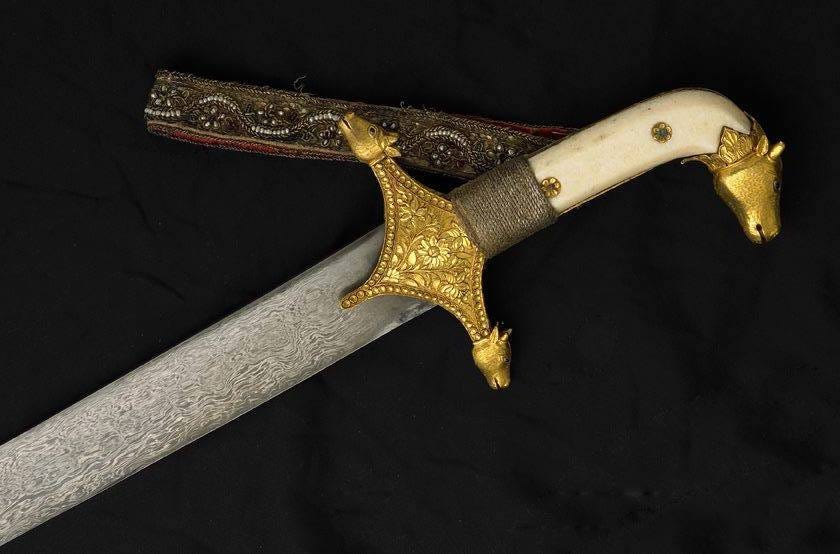
And finally, even fashion seemed to provide an example. In the 1800s, Victorian women had to deal with corsets and crinoline, as shown below, to provide structure to a skirt.

By comparison, Indian women’s apparel stood out for its freedom of movement and relative lack of structure.

So it seems like there could be something to rigidity being a cultural difference rather than a clear step forward for technology. Maybe stiffness dominates because of its historic usefulness is certain areas, like firearms. I don’t much care for the “East” v. “West” part of the argument, since there are counterpoints. It also discounts the Americas and its flexible designs, like the baidarka. What’s interesting to me is that the current, globalized engineering culture seems to have accepted stiffness as an advancement and flexibility as a more backwards approach. I disagree with that wholeheartedly. Keeping an open mind to the “bend but don’t break” philosophy that nature herself favors could open the door to a host of unique, lightweight designs.
Damascus steel still has me baffled until today. I heard (..) one of the most accurate descriptions of what it was and how it was made is actually in a novel - The Baroque Cycle by Neal Stephenson
Brings to mind the lateral flex engineered into Moto GP bikes. When the bike is leaned hard into a turn, the suspension is now (nearly) parallel to the ground, thus the flex acts as vertical suspension while cornering.